FLYING-CAM, ein weltweit führendes Unternehmen in der Entwicklung und Herstellung unbemannter Hubschrauber und ein Pionier im Bereich professioneller Drohnen-Videodienste, feierte sein 30-jähriges Bestehen mit der Weltpremiere von Discovery, seinem brandneuen unbemannten Luftfahrzeugsystem (UAS).
Das in Belgien ansässige Unternehmen beschloss, sich an CRP Technology und seine fortschrittlichen 3D-Drucklösungen mit Verbundwerkstoffen zu wenden, um eine Komponente des Flugzeugs zu bauen.
Das Projekt
Die Discovery ist ein unbemanntes Flugzeug mit Einzelrotor und einem maximalen Startgewicht (MTOW) von 75 kg und damit das bisher größte und vielseitigste System von FLYING-CAM, mit außergewöhnlichen Merkmalen in Bezug auf Widerstandsfähigkeit und Autonomie.
FLYING-CAM hat CRP Technology mit der Herstellung des Heckrotor-Getriebegehäuses der Discovery beauftragt. Dies ist das Hauptgehäuse, das am Hauptausleger des Hecks befestigt ist.
Emmanuel Previnaire, Gründer und CEO von FLYING-CAM, erklärt: „In Anbetracht des Potenzials, das Drohnen für den zivilen Markt bieten, und angesichts des wachsenden Interesses am Fliegen außerhalb der Sichtweite (Beyond Visual Line Of Sight, BVLOS) war es unserer Meinung nach an der Zeit, eine Drohne zu entwickeln, die nicht nur schöne Bilder für Filme, Fernsehsendungen und Werbespots aufnehmen, sondern auch Daten für andere industrielle Zwecke sammeln kann.
Das Ergebnis war die „Superdrohne“ mit dem Namen Discovery, die mit hochmodernen Sensoren ausgestattet ist, dank der die Plattform an viele professionelle Zwecke angepasst werden kann, die von der Unterhaltungsindustrie über die nationale Sicherheit bis hin zur Erdbeobachtung und hochpräzisen Fernerkundung im Allgemeinen reichen.“
Um eine solch einzigartige Drohne zu entwickeln, musste FLYING-CAM auf einen Anbieter von hochmodernen Technologielösungen zurückgreifen, der in der Lage ist, hohe Qualitätsstandards bei der Herstellung von sicheren und zuverlässigen Komponenten einzuhalten. Aus diesen Gründen entschied sich FLYING-CAM für die Lösungen von CRP Technology mit dem Verbundwerkstoff Windform und dem 3D-Druck.
Im 3D-Druck hergestelltes Heckrotor-Getriebegehäuse
CRP Technology erhielt die Aufgabe, eine Schutzstruktur für die Heckrotorantriebe und die GPS-Antenne herzustellen, die leicht aber gleichzeitig physisch und aerodynamisch steif sein sollte.
In Anbetracht der hohen Anforderungen von FLYING-CAM entschied sich CRP Technology daher für den professionellen 3D-Druck (speziell das Selektive Lasersintern) als Herstellungsverfahren und Windform® XT 2.0 als Konstruktionsmaterial.
Windform® XT 2.0 ist ein kohlefaserverstärkter Verbundwerkstoff auf Polyamidbasis, der sich besonders für die Herstellung von leistungsstarken Komponenten für anspruchsvolle Industriezweige wie Motorsport, Luft- und Raumfahrt und UAVs eignet.
Bei der Wahl des Materials wurde sehr sorgfältig vorgegangen: „Das Teil“, fügt Emmanuel Previnaire hinzu, „sollte an den Heckausleger geklemmt werden und auch die Karbonplatte tragen, die als Bodenschutz für den Heckrotor dient. Aus diesem Grund war eine gute Belastbarkeit erforderlich.
Die Festigkeit der Klemmung hängt von den Fähigkeiten des Konstruktionsmaterials ab. Wir haben uns für Windform® XT 2.0 entschieden, da es ein gutes Verhältnis zwischen Gewicht und Festigkeit bietet.“
Die mechanischen und thermischen Eigenschaften der Windform®-Materialien sind eng mit den Eigenschaften des 3D-Druckverfahrens verbunden. In der Tat führt die Kombination von beidem zu unvergleichlichen, hochtechnologischen, im 3D-Druck hergestellten Teilen, die sofort einsatzbereit sind.
Diesbezüglich weist Emmanuel Previnaire auf Folgendes hin: „Die innovativsten Aspekte des 3D-Drucks mit den Windform-Materialien von CRP Technology sind die Designfreiheit, die für aerodynamische Zwecke wichtig ist, und die Möglichkeit, komplexe und funktionale Teile in einem Stück herzustellen – wie Kabelkanäle mit einem starken Befestigungspunkt im Inneren. Das ist ein Mehrwert, der perfekt zu unseren Zielen und Standards passt.
Insbesondere der 3D-Druck und die Windform®-Materialien ermöglichen die Herstellung von Hohlkörpern mit vielen funktionalen Details, wie z. B. die Integration von Befestigungsmuttern und Kabelbefestigungspunkten.“
Die Bedeutung des richtigen Technologiepartners
Die Systeme von FLYING-CAM haben sich im Laufe der Jahre weiterentwickelt, um mit den immer anspruchsvolleren Marktanforderungen Schritt zu halten.
„Früher“, so Previnaire, „konnte man mit einem Produkt 15 Jahre lang im Geschäft bleiben. Heute muss man alle sechs Monate ein Update vornehmen. Aus diesem Grund haben wir eine Plattform entwickelt, die mit den Anforderungen der sich ständig weiterentwickelnden Technologie Schritt hält.
Und um ein Höchstmaß an Zuverlässigkeit, Sicherheit, Präzision und Anpassungsfähigkeit für eine Vielzahl von Aufgaben – wie z. B. Kartierungen und Inspektionen – zu erreichen, verlassen wir uns auf Partner, die nicht nur modernste technologische Lösungen anbieten, sondern auch Vorreiter für technologische Innovationen auf höchstem Niveau sind, und dazu gehört CRP Technology.“
„Die Zusammenarbeit mit CRP Technology begann bereits vor vielen Jahren mit der Herstellung von SARAH 3.0, unserem unbemannten elektrischen Senkrechtstarter (VTOL), der nun durch SARAH 4.0 ersetzt wurde.
CRP Technology hat mehrere Komponenten hergestellt, darunter die tragende Struktur, das Luftkühlsystem und das Leitwerk.“
SARAH ist wie Discovery eine hochmoderne unbemannte „intelligente“ Lösung für die Luftfahrt, die nur durch die Beherrschung aller damit verbundenen Technologien und Fähigkeiten umgesetzt werden kann.
Im Jahr 2014 wurde FLYING-CAM eben für die Entwicklung von SARAH mit dem technischen Oscar® Scientific and Engineering Award ausgezeichnet.
Previnaire erklärt: „Wir haben bereits zwei Oscars® und einen Emmy Award® gewonnen; diese spezielle Sci-Tech-Auszeichnung erfüllt uns mit Stolz, da sie eine weitere Bestätigung unseres professionellen Ansatzes ist, der seit jeher nach Spitzenleistungen strebt, indem er die Grundsätze der zivilen Luftfahrt und der Flugnavigation in die Praxis umsetzt. Diese Methodik wird nicht nur die Ingenieure des Unternehmens weiterhin zu Höchstleistungen anspornen, sondern sie dient uns auch als Richtschnur bei der Auswahl von Fertigungspartnern, die mit Fakten beweisen müssen, dass sie auf der gleichen Wellenlänge liegen wie wir.
Die Zusammenarbeit mit CRP Technology begann mit SARAH und hat sich bis heute fortgesetzt.“
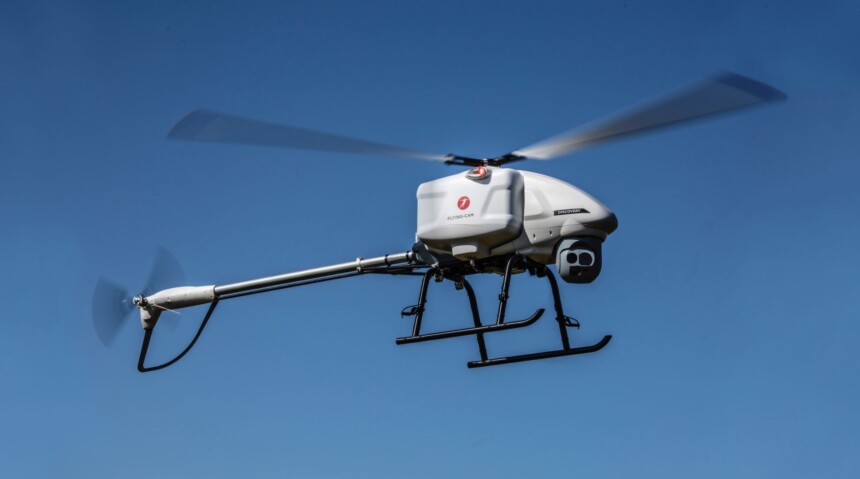